Building a successful manufacturing operation is a complex endeavor that involves understanding the intricate dynamics of production, people, and processes. In today’s competitive market, manufacturers cannot overlook the key pillars that support operations, nor can they ignore the technological advancements that offer a competitive edge. Below, we delve into best practices and strategies that can catapult manufacturing ventures to new heights. Keep reading to discover the core elements that will help you lay the groundwork for a thriving manufacturing business.
Leveraging Technology for Enhanced Manufacturing Efficiency
Today’s manufacturing landscape is inextricable from the technological innovations that continue to evolve. From automation and robotics to advanced data analytics, technology offers unparalleled opportunities for efficiency gains. These technologies can streamline repetitive tasks, minimize human error, and ensure that operations can run 24/7 without the constraints of human endurance.
Digitalization, converting information into a digital format, has drastically transformed the manufacturing industry. It assists in capturing real-world processes in digital form, enabling simulation, analysis, and enhancements that were previously inconceivable. For example, with digital twin technology, manufacturers can create virtual replicas of their production lines to test and refine processes before implementing physical changes.
Adopting ERP solutions is a manufacturing operation’s most transformative strategic decision. Enterprise Resource Planning systems offer an integrated approach to managing business processes, from inventory management to customer relations. These comprehensive systems improve communication, streamline workflow, and provide real-time data that empower managers to make informed decisions that align with the company’s objectives.
Artificial Intelligence (AI) and Machine Learning (ML) have found their place in modern manufacturing, too. They contribute to predictive maintenance, anticipating machine failures before they occur and minimizing downtime. AI and ML enhance quality control by analyzing large datasets to identify patterns and variances that may indicate a decline in product quality or production inefficiencies.
Strategies for Workforce Development and Skills Training
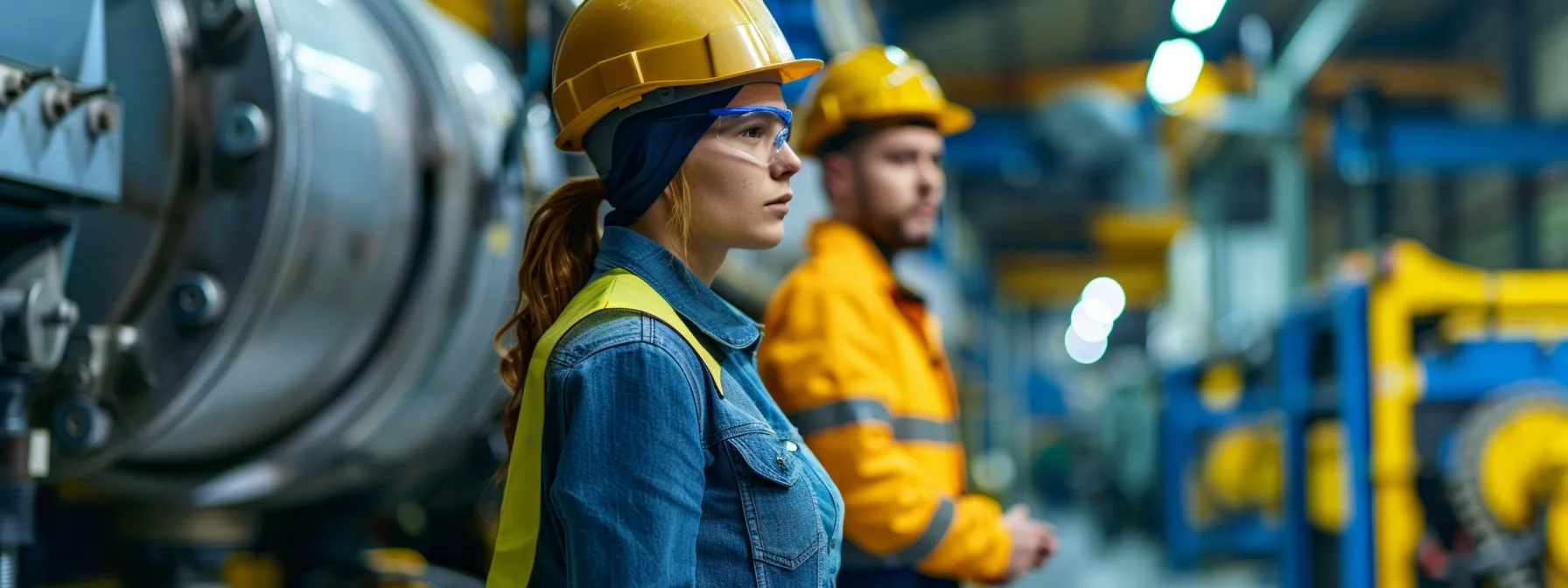
The backbone of any manufacturing operation is its workforce. As technology advances, the demand for skilled labor to work alongside and maintain sophisticated machinery also increases. This necessitates a strategic approach to workforce development and skills training to ensure employees can meet the demands of evolving manufacturing environments. Investing in employee education and upskilling boosts production efficiency and enhances employee satisfaction and retention.
Apprenticeship programs are a time-honored strategy that can bridge the gap between theoretical knowledge and practical skills. They enable experienced workers to pass their expertise to the new generation, ensuring that core competencies and craft techniques are not lost. Apprenticeships are particularly valuable in specialized manufacturing sectors where bespoke skills are at a premium.
Cross-training strategies are becoming increasingly popular to create a more resilient and flexible workforce. Manufacturers can more easily adapt to shifting market demands and workforce availability by teaching employees multiple aspects of production and various roles.
Moreover, incentives for continuous learning and improvement are crucial for keeping the workforce motivated and at the forefront of industry innovations. Providing workers with opportunities to attend conferences, workshops, and seminars can yield a tremendous return on investment, as these activities can spur innovation and operational improvements from within the company’s ranks.
Compliance and Quality Control in Manufacturing Management
Manufacturers’ compliance with industry standards and regulations is non-negotiable. It is a matter of legal obligation and critical to ensuring safety and customer confidence. A systematic approach to compliance helps avoid costly recalls and penalties. Implementing regulatory change management processes ensures that operations consistently align with the latest laws and industry guidelines.
Quality control mechanisms are integral to compliance; they help maintain the integrity of the manufacturing process. Quality control protocols must be rigorous and replicable, from raw material inspections to final product testing. Utilizing statistical methods and software to monitor quality can provide early warnings for potential non-compliance and safeguard against defective products reaching the market.
Training staff in compliance and quality is equally as important as the systems themselves. Employees must understand the legal requirements to which their roles are subject and the company’s internal quality standards. Creating a culture that prioritizes compliance and quality can often lead to a more conscientious and proactive workforce, which is an asset to any manufacturer.
Regular audits and feedback loops are valuable for continuing enhancement. These tools can help your company pinpoint areas for improvement and ensure that quality and compliance are living aspects of the manufacturing process rather than static targets. By doing so, manufacturers can demonstrate their commitment to excellence and build a reputation for reliability and quality in their industry.
Overall, successfully building and maintaining a manufacturing operation requires a strategic blend of technology, workforce development, and stringent compliance measures. By focusing on these core elements, manufacturers can enhance efficiency, adapt to industry changes, and establish a reputation for quality and reliability.
Read More: Passages Malibu Logo: Symbol of Healing and Transformation